铣刀齿数多,可提高生产效率,但受容屑空间、刀齿强度、机床功率及刚性等的限制,不同直径的可转位铣刀的齿数均有相应规定。
为满足不同用户的需要,同一直径的可转位铣刀一般有粗齿、中齿、密齿三种类型。
选择齿数时,首先要考虑机床刚性与负载,齿数过高,切削力大,会导致设备负载超载或者工件变形.
其次,要考虑刀具刃口负载和排屑,参考刀具推荐的每齿进给量原则,并根据加工质量判断是否有排屑问题。
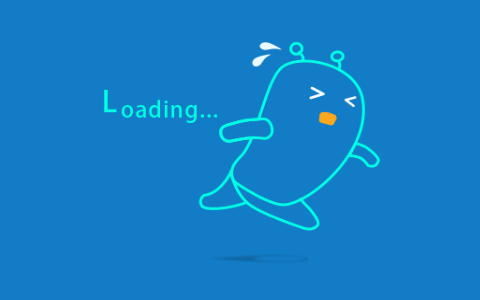
干切削加工,是一种加工过程不使用或微量使用切削液的加工技术,一种对环境污染从源头进行控制的清洁环保制造工艺。
有人认为,相比于连续加工的车削,断续加工的铣削似乎更加适合使用干切削技术,不但不必担心切屑断屑问题,甚至还可以减少施加在刃口上的、冷热交替的热冲击。
但是,实验表明,干切削刀具寿命明显低于湿切削,且刃口以破损失效为主。
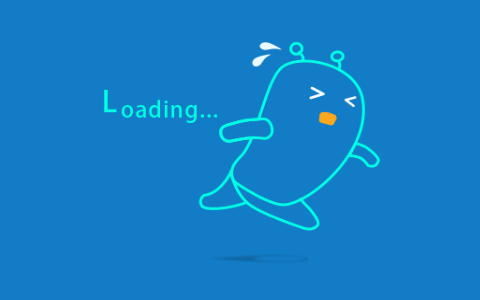
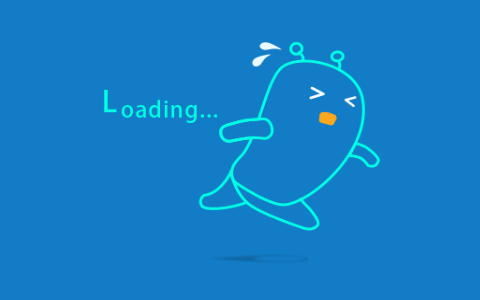
|
对策 |
机床自身的刚性 |
1、减小切深与进给。 2、选择切削力小的切刃形状刀具。 |
工件的形状与夹紧刚性 |
1、消除工件支承面的变形,起伏。 2、对切削力作用面增加支承。 |
刀柄系统 |
1、刀柄与刀具安装部保持清洁,清理异物。 2、尽量减少伸出长度。 |
刀具本体 |
1、排除刀片安装面异物。 2、刀片的夹紧零件要定期更换。 3、减少齿数,选不等分刀齿铣刀。 4、减少刃口修磨量。 |
刀具的切削性能 |
1、选取耐磨性好的刀具材料。 2、选前角大的刀片减少切削力。 3、减少偏角,减少径向力。 |
切削条件的不适 |
重新选择切削速度、进给量和切深。 |
原因 |
对策 |
刀具的磨损 |
选耐磨性好、红硬性高的材料。 |
切刃振摆 |
用通用面铣刀时加装修光刃刀片。 采用以刀尖作基准的铣刀。 |
切削速度过低 |
提高切削速度→切削力降低→抑制工件弯曲变形。 |
正确使用修光刃刀片,可以提高表面粗糙度,需要注意的是修光刃相对于普通刀片的高度差。
参考实验数据,如下图所示,切削速度提高,加工表面粗糙度下降,每齿进给量过高,表面粗糙度恶化。
将“修光刃影响”和“切削参数影响”设计到同一个实验中,因素影响对比结果如下图所示。
波度,是指衡量工件表面高度起伏的指标,通常是指测量平面中最高点和最低点的高度差,如下图所示。
原因 |
对策 |
机床或者工件夹紧刚性差 |
消除工件安装面的变化,增强支撑刚性。在切削力作用方向加支承,尽量减少伸出量。 |
工件形状不均匀 |
减少刃数,减少总切削力,或者减少余偏角,减少径向切削力。 |
刀具的切削性能 |
选前角大、切削力小的刃形。 |
切削条件的不适 |
重选切深进给量。 |
铣削平面时,受到加工路径和断续加工的影响,会产生不同程度的翻边和毛刺,如下图所示。
相应地,铣削刀具参数与翻边毛刺的关系如下图所示:
翻边毛刺的原因和对策,如下表所示:
原因 |
对策 |
刀具的切削性能(锋利程度) |
减小余偏角,减少径向力; 减少刃口修磨量,保持刃口锋利。 |
刀具本身角度 |
选择前角大切削力小的刃形 |
切削条件的不适 |
重新选择进给量和切深 |
特别是加工硬度较低的材料时,在边缘位置,未被切削的材料会产生塑形变形而形成翻边,如下图所示。
这里介绍一种“去毛刺刃”,其原理就是加大刀片的前角,以图减少切削力,将边缘金属材料切除掉而不是挤压成翻边,如下图所示。
去毛刺刃因为刀尖强度差,可与通常刃组合在一起加工,效果好,例如将形成最终表面的修光刃刀片,设计成大正前角,实现“去毛刺刃”的功能。
介绍这种“去毛刺刃”只是为了拓展大家解决问题的角度,但是作者认为,大前角刀片在实际加工过程中,特别是断续切削、强烈冲击工况的铣削中应用,效果不一定理想。
本文转载来自【机加工程师】,仅供大家学习交流,如侵权请联系站长删文。