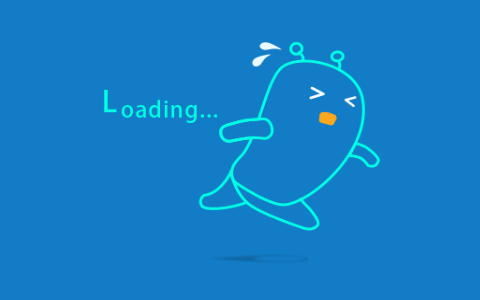
FANUC国内某客户生产的一台立式加工中心使用了FANUC电主轴,在跑机运行4~5小时后,出现SP9012:DC link过电流报警。低速到高速绕组切换时主轴电机负载约为180%~200% ,高速到低速绕组切换时负载约为120%~150%。电机正常运转时电流平稳。现场还有另外两台机床,均未出现此情况。
电主轴:A06B-1673-B100#S31S (BiI 112M/15000)
主轴放大器:A06B-6220-H026#H600(αiSP 26-B)
主轴编码器:A860-2150-T401(αiBZ 256λ)
2)测量电主轴、接触器的绝缘电阻、相间电阻、相地电阻,检查动力线
使用电表测量电机、接触器的绝缘电阻,符合要求,不存在短路;重新拧紧动力线,并确保连接正确,无短路。使用毫欧表测量电主轴的绕组阻值,各相绕组阻值均衡。虽低于FANUC推荐值,但与现场正常机床一致,排除电主轴绕组问题。
检查各管脚接线,并重新焊接屏蔽层,将反馈线从电柜单独走线。测量反馈信号,整体情况较好,在绕组切换时有轻微波动。
排查完外部接线后,对主轴参数进行初始化,设置NO.4019#7=1,重新上电,然后手动输入电机参数,确保参数正确。
绕组切换时,梯图中有切换延时计时器,更改延时时间,保证无短路。
绕组切换时,FANUC要求接触器的额定电流至少是电机的短时额定电流(S2曲线),现场使用的是65A接触器,但改用100A接触器后仍不能解决问题。
在排除硬件、参数问题后,根据以往的经验,绕组切换时由于电流冲击较大,且对时序有严格要求,故对绕组切换进行排查。
由于高低速绕组的INORM系数不同,所以分两次监测,图1是速度变化时,按高速绕组测量的电流值。图2是速度变化时,高低速绕组测量的电流值对比。红色为低速绕组。
可以看到从0 rpm升速到2000 rpm的过程中,低速绕组的电流为400A,在2000 rpm转速稳定后,低速绕组电流为25A。从2000 rpm升速到5000 rpm左右进行绕组切换,在350ms内电流从200A下降到140A,绕组切换完成后,有一个短暂的冲击,约为200A。
从5000 rpm到7000 rpm,电机以125A的电流加速到7000 rpm。在7000 rpm转速稳定后,高速绕组电流约为10A。
从7000 rpm下降到5000 rpm时,高速绕组切换为低速绕组,电流约为75A。切换完成后,在300ms的时间内电流从200A上升到400A。
从以上电流监测看到,在绕组切换时,电流变化非常大,很有可能是导致该报警的主要原因。
原梯图仅使用低速绕组确认信号G71.7来确认绕组切换状态,根据主轴参数说明书,应满足以下时序:
监测信号时发现,从低速向高速绕组切换时,高速绕组接触器Y1.2指令晚于F46.3,故可能造成绕组切换未完成,而系统参数已经选择为高速绕组的情况。而从高速到低速绕组切换时,低速接触器Y1.3先于F46.3变化,故可以保证参数与绕组状态一致。
修改参数NO.4014#3=1,使用G72.7作为高速绕组切换确认信号,根据主轴参数说明书,应该满足以下时序:
再次测量Y1.2和F46.3的关系,此时高速绕组接触器先与F46.3吸合,时序正常。而从低速到高速切换时的时序不受影响。
按照FANUC说明书中推荐的方式,使用“根据速度指令切换的方法”,并设置NO.4014#3=1,使用G72.7后,测得的电流数据。可以看到,升速之前,先进行了绕组切换。
图6 使用“根据速度指令切换”和G72.7的电流波形
为了更具体地观察切换电流,测试了从0 rpm到4000 rpm再到7000 rpm的升降速过程。
改用原始梯图,使用“根据实际电机速度的切换方法”,并使用G72.7后,测得的电流数据。可以看到,从4000 rpm升速到7000 rpm的过程中,在5000 rpm左右进行绕组切换。
图9 使用“根据电机速度切换”和G72.7,原梯图0-4000-7000 rpm升降速过程
使用原梯形图,将NO.4014#3设为0,再次测试绕组切换时的电流,电流基本一致,只是在5000 rpm到7000 rpm绕组切换后期,电机电流有一个大幅度的冲击。
图10 不使用G72.7,原梯形图绕组切换出现电流冲击
根据以上分析,此次偶发SP9012报警的原因是绕组切换时,有微小电流冲击,机床长时间运行后,放大器检测到异常电流,故发出SP9012报警。
解决办法是设置NO.4014#3=1,修改梯图,使用G72.7作为高速绕组确认信号,可以抑制电流冲击。
– END –
本文转载来自【北京发那科】,仅供大家学习交流,如侵权请联系站长删文。